Turning a tsunami of plastic pollution into the world’s cleanest power – MAGAZINE EXCLUSIVE (SPONSORED CONTENT)MAGAZINE EXCLUSIVE (SPONSORED CONTENT)
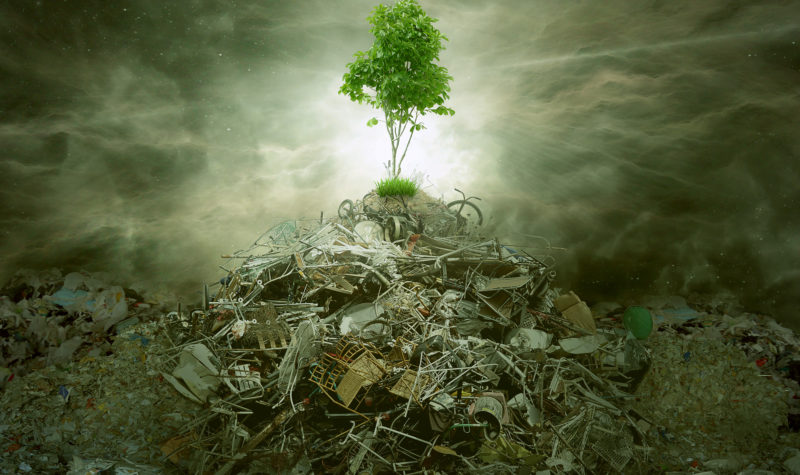
MAGAZINE ARTICLE
This article first appeared in Issue 42 of Master Investor Magazine.
Click here to download the article as a printer-friendly PDF
![]() Get this article and many more – for free! |
What are the following companies doing to which you should pay close attention?
Alstom, Audi, BMW Group, China Energy, Daimler AG, Great Wall Motor, Honda, Hyundai, Nippon Oil & Energy, Shell, Toyota Tsusho – among others.
Each is investing in hydrogen. Extensively.
In fact, each is an original member of the Hydrogen Council, formed in Davos, Switzerland, in 2017, for the express reason of accelerating the development of the “hydrogen economy.” They’ve made a $10.7 billion… yes, billion… commitment to building out the necessary components of a functional, cost-effective, hydrogen ecosystem. To date, 39 major multi-national companies have joined the Hydrogen Council to help shape the future of energy.
Let’s talk about hydrogen
Hydrogen. The single most abundant element in the universe. A gas that when combusted generates water vapour. It’s the substance that powers the sun. It’s quite literally solar power! And it’s considered by many to be the holy grail of energy and power production for the future.
It’s believed that using hydrogen to fuel transportation can help reduce worldwide CO2 emissions by more than 25% by 2050.Industrial transport. Public Transportation: trains, buses, ships, airplanes. And of course, our automobiles. Hydrogen, as a fuel, is being adopted by more and more companies every day. Walmart uses hydrogen to power its fork-lifts. Anheuser Busch has placed an order for 800 HGVs for its US operations. And Toyota is focusing on decarbonising the Port of Los Angeles to reduce diesel pollution and particulate matter in the air.
It’s the most plentiful element in the universe. The entire universe. However, it’s not found in ‘deposits’ or ‘pools’ or ‘mines’ here on Earth, and acquiring it in its purest form is a relatively expensive process. It’s expensive economically and it’s expensive environmentally. 95% of all hydrogen is derived from natural gas reformation. But the challenge is that between 12 and 16 tonnes of Carbon Dioxide is produced for every tonne of hydrogen generated from natural gas. Natural gas reformation is currently the only industrial scale producer of hydrogen on earth. But it’s also a massive producer of greenhouse gases as an unfortunate by-product. Unless Carbon Capture and Sequestration (CCS) technologies catch up, large scale, low-carbon hydrogen is likely to be a pipedream – and in more ways than one.
Would you like to learn more about PowerHouse Energy? Meet them at ‘Master Investor in focus: Investing into alternative energy’ on 11 October 2018 in London.
A selected few free tickets are still available. Book early to avoid disappointment. |
The least expensive method of transporting hydrogen is, of course, by pipeline. However, very few hydrogen pipelines exist, and they are extremely limited. One can’t simply repurpose our standard natural gas or oil pipelines to accept hydrogen. Hydrogen degrades and embrittles the metal and, therefore, requires specialised pipelines. These are very expensive to install, and it will take decades to achieve an equivalent coverage to today’s gas and oil pipelines. If we can make CCS work and install the necessary pipelines to transport hydrogen and capture carbon dioxide, then we’ll be able to tap into the grid and have truly mass distributed hydrogen.
One of the biggest costs, both economically and environmentally, associated with hydrogen is the cost of distribution. Hydrogen is enormously expensive to transport and move from where it’s produced to where it’s needed and used. An entire lorry filled with industrial canisters of hydrogen – the entire forty-four-foot trailer – can only transport less than a single tonne of hydrogen. An empty three axel “tube trailer” and tractor for hydrogen transport weighs 37,500kg. That entire trailer only transports 321kg of hydrogen!
Ultimately, we’ll likely get to fully distributed (meaning available at point of use), cost-effective, hydrogen. But, until then, we can’t afford to let hydrogen lie dormant. It’s the ultimate low-carbon fuel. It’s the cleanest fuel on Earth!
But how do we get low carbon hydrogen where we need it? How about electrolysis?
Separating pure hydrogen from water by using electricity seems like the ideal mechanism from which to derive hydrogen in a distributed manner. Many of us did so in school science experiments. But it’s far from perfect. For the hydrogen to be truly “green”, the electricity used in the process must come from “alternative sources.” In other words, from solar, wind, or tidal electrical generation. The challenge is that there simply isn’t enough alternative energy to power electrolysis to create green hydrogen. In fact, in reality, the CO2 footprint that is ostensibly being replaced by the hydrogen produced under typical processes is simply being moved back to the electrical grid – where in the US, over 62% (UK: 51%) of electricity is still being created by burning coal and other fossil fuels. Less than one quarter of UK electricity is being generated by renewable sources. The “Renewable Target” for the UK is only 30% by 2020. So, while electrolysis is certainly a part of the equation to help build the hydrogen economy, it’s not the panacea that some believe it to be.
Furthermore, the current cost of retail hydrogen is between £10-12 per kilo – several times the price of a litre of petrol or diesel.
When the price of hydrogen achieves parity with petrol or diesel, and ubiquitous environmentally-friendly electricity is universally available, then electrolysis can begin to have an impact.
Now let’s talk about plastic…
Waste elimination, particularly for unrecyclable plastics and end-of-life tyres (two of the biggest challenges faced by the waste management sector), is also a major global challenge. In fact, as has been widely reported in the world’s media over recent months, there is a tsunami of waste plastic that is growing ever larger in size as each day goes by.
An expedition by National Geographic last year discovered a previously unknown patch of floating and sub-surface plastic off the coast of Chile. That patch alone is estimated to be three times larger than the entire UK.
There are now six massive known “plastic patches” in gyres (areas where the ocean currents converge) in our oceans. The plastic problem has begun to kill marine life and cripple the oceanic ecosystem. And each year, over eight million more tonnes of plastic finds its way into our rivers, streams and, ultimately, our oceans.
Next year, even amid the calls to curtail single-use plastics, increase plastic recycling and stop this impending disaster, there will be more virgin plastic produced than the weight of every man, woman and child on our planet.
Plastic is here to stay. It’s a “miracle product” in many ways. It has increased food safety and extended the shelf-life of many products. It is the basis of our mobile phones, our televisions, our computers. It allows hospitals to deliver oxygen and medication, and to literally save patients’ lives. And yet, it’s wreaking havoc on our environment.
But now there’s a viable, efficient, and straight-forward solution to this conundrum. One which combines a commercially available technology that can reduce global plastic waste, and which enables the economically viable production of hydrogen.
PowerHouse Energy Group Plc has pioneered a proprietary technology platform that enables its customers to extract pure hydrogen from the wave of plastic pollution facing our world.
And it does so at a price on par with diesel or petrol!
Its technology DMG® (a process centred on ultra-high temperature thermal conversion) creates EcoSynthesis Gas, from which a stream of 99.999% pure, road-fuel quality hydrogen can be derived, as well as a number of other useful chemical products.
And, critically, for hydrogen production, the DMG® technology generates between 12 and 16 times less CO2, on a like-for-like comparison, to hydrogen that is generated from natural gas.
The other components of EcoSynthesis Gas, produced by customers utilising the DMG® technology platform, is that it can be used as chemical precursors for industry, or cleanly combusted to run highly efficient electrical generators for private usage, or for sale back to the National Grid. And the beauty is that the flexibility of the DMG® technology allows for the precise tuning of the EcoSynthesis output to be adjusted to meet individual customer requirements.
The DMG® technology platform is well positioned to address the issue of reducing waste, particularly plastic and end-of-use tyres, as it uses these and other wastes as the feedstock for producing EcoSynthesis Gas.
Achieving the elimination of tonnes of waste in an environmentally responsible and commercially viable basis allows us to turn our waste into a friend rather than an enemy.
Other attributes that underpin the power of the DMG® thermal conversion technology are its modular design, small footprint, and ease of operation. Many of the components around which the DMG® technology is based are already widely used, well established over many years, and technologically proven. PowerHouse has leveraged a unique integration of these components with the addition of some clever and compelling proprietary IP.
Requiring less than half an acre of land, a single DMG® thermal conversion powered module can process between 5 and 40 tonnes of waste plastic (a single lorry-full of plastic is approximately 25 tonnes). At its nominal operational size of 25 tonnes per day, it can produce – in a single day – enough hydrogen to fuel 40 to 50 lorries or buses for 300 miles each, and provide electricity to over 2,000 homes for 24 hours. All on a postage stamp size lot.
PowerHouse Energy’s DMG® technology has been undergoing extensive testing and refining at the University of Chester, Thornton Science Park Energy Centre, where it was successfully integrated with the Energy Centre’s micro-grid this year. The EcoSynthesis Gas produced by the Research Demonstrator has been independently analysed and its hydrogen component verified. The data acquired during the conversion of native plastics, mixed plastics, and tyre crumb has been fed into sophisticated engineering modelling software and the commercial design of the DMG® technology platformhas completed the FEED (front-end engineering design) stage of development.
It hasn’t been an easy journey…
But as the saying goes, “if it was easy, everyone would have done it!” PowerHouse has been engaged in over 18 years of technology exploration, research and development, extremely promising advances, and inevitably a few disappointing outcomes and delays along the way. But that is the path of nearly every disruptive technology. And, finally, DMG® has reached the technology readiness level necessary for it to start driving market adoption. The commercialisation process is now fully underway.
The next step is to build the first commercially operational system powered by the DMG® technology platform which will become a “show piece” and be used to demonstrate its efficacy and utility to future customers.
Having completed the FEED for the DMG® System, planning and permitting applications are under way, and PowerHouse is currently engaging with early-adopter, and potential referencecustomers, who have an interest in purchasing and putting the DMG® System to use at their own facilities. Additionally, PowerHouse is working with a number of project development partners around the globe to establish DMG®internationally.
The DMG® technology platform enables a customer, on an attractive commercial basis, to contribute to the elimination of plastic pollution while achieving something the Hydrogen Council, and the world at large, is aching for: truly distributed hydrogen – produced where it’s needed, at a cost that is the equivalent of petrol or diesel.
The PowerHouse Energy Group’s enabling DMG® technology is ready to deliver a means to help clean-up our environment while allowing its customers to capture the pure, clean, power of this most miraculous of elements – hydrogen.
A truly green company and a business that is underpinned by a regulatory environment that is only going to get tougher in regards of how plastic waste is disposed of in an environmentally friendly way,PowerHouse Energy’s objective is to harness the true power of literally wasted resources by delivering the DMG® platform to be embedded within the consumer and industrial landscape.
High efficiency and low-carbon. Responsible, proven, environmental credentials. Economically compelling operations. These are the demands of the new world order – they command a social, political and commercial premium.
DMG® addresses these demanding criteria today, allowing PowerHouse to be poised to achieve broad and sustainable commercial adoption around the globe.
To learn more about PowerHouse Energy Group plc, go to: www.powerhouseenergy.net.
PowerHouse Energy Group Plc is listed on the AIM Market of the London Stock Exchange and trades under the ticker symbol: PHE.
About Keith Allaun
Keith Allaun has a background in alternative energy, venture capital and management consulting. Mr Allaun has worked with leading companies in emerging technologies for over 25 years. Educated at Stanford University in Palo Alto, CA, Mr Allaun possesses an extensive background in management and brings a wealth of results-driven experience to PowerHouse Energy Group. Mr Allaun has helped build or revitalize dozens of companies & organizations throughout his career including PowerHouse Energy, Apple, Yahoo, Amazon and Hewlett-Packard.
![]() |
Comments (0)