Battery Charge
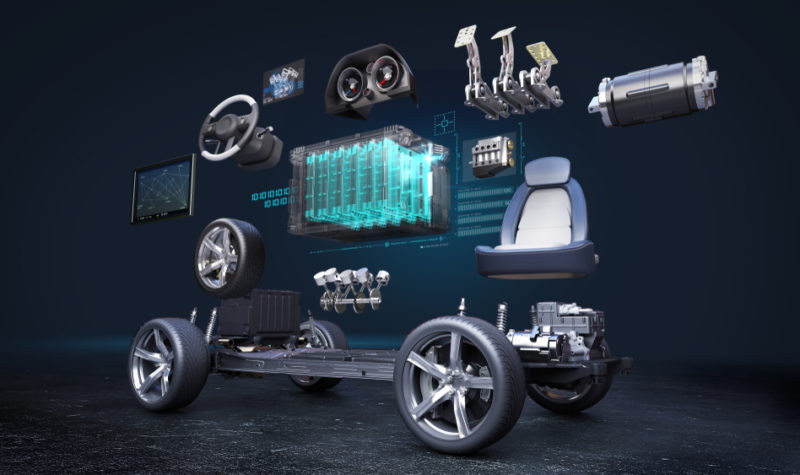
Giga-factory go-ahead?
In late January, UK start-up Britishvolt unveiled plans to build a £2.6 billion factory in Blyth, Northumberland, which will manufacture 300,000 lithium-ion electric vehicle batteries a year. Construction on the plant could start as soon as this summer in which case production would begin in 2023. The plant will create 3,000 jobs on-site and 5,000 more in the supply chain.
Britishvolt, founded by Orral Nadjari and Lars Carlstrom (who has since stepped down) last year, has literally come out of nowhere. Mr Nadjari originally favoured a site on a former RAF air base near Cardiff airport in south Wales. Reportedly however, the Welsh government was too slow to respond to Britishvolt’s ambitious timetable. The preferred location in Blyth is on the site of a disused coal-fired power station and has good transport links. Mr Nadjari claims that Britishvolt is in advanced discussions with leading automotive manufacturers.
Then this week it was announced that Coventry airport could become home to a second giga-factory. The site has been earmarked by the West Midlands metropolitan county which is inviting potential developers to bid. Coventry is already home to Jaguar Land Rover (JLR) (owned by Tata Motors of India), Aston Martin Lagonda (LON:AML), and BMW (ETR:BMW). The elected metropolitan mayor, Andy Street, describes himself as obsessed by the EV giga-factory project. Andrew Bell, CEO of Regional and City Airports (private) is also an enthusiast.
While this is all good news for the UK (or will be if these plants do materialise), Andy Palmer, the former CEO of Aston Martin said last month that Britain will have to build at least four giga-factories over the next five years, or risk the collapse of its automotive industry – because manufacturers will locate where the batteries are. Britain is behind the other major car-making powers in this domain. China and the USA have sizeable production pipelines while the EU is expected to build at least 11 new giga-factories by 2030. Many established players in this sector such as LG Chem (KRX: 051910) have opted to establish their EV battery plants in Europe.
Electrification accelerates
On Monday (15 February) JLR announced that all Jaguar models would be electric from 2025 – five years ahead of the UK government’s self-imposed deadline whereby no new petrol or diesel cars will be sold from 2030. JLR also said that it would launch its first battery-powered Range Rover in 2024. The firm pledged to maintain its British manufacturing base as it transitions to all-electric models; however, car production at the Castle Bromwich plant will end after 44 years.
Thierry Bolloré, JLR’s CEO who took the reins last September, said that the historic plant – where Spitfires were manufactured during WWII – would be repurposed. The firm’s strategy is apparently to focus on high-end vehicles, implying that the firm will go upmarket to compete with Aston Martin and Bentley (owned by Volkswagen (ETR:VW)). The company is also working on the development of hydrogen fuel cell-powered vehicles.
Lotus is investing £100 million in its plant at Hethel, Norfolk, in order to build a new range of electric sports cars. The company, whose brand evokes huge customer loyalty, is owned by Chinese automotive manufacturer Geely (HKG:0175) (which also owns Volvo and black-cab maker LEVC) and the Malaysian firm Etika Automotive. Lotus will take on another 250 staff in addition to the existing 1,500 it already employs. Last month Lotus appointed Matt Windle as CEO. Mr Windle was poached by Tesla from Lotus back in 2005 but now returns to Norfolk to share his extensive knowledge and experience. Last year, Lotus sold just 1,519 cars – and managed to lose £14 million on revenues of £96 million.
A recent poll by the RAC found that the number of people planning to switch from internal combustion engine (ICE) powered vehicles to EVs jumped from just six per cent in 2019 to nine percent last year. It seems, however, that purchase cost is still the main drag on switching. The second-hand market for EVs is still very thin. The other drag is that people fear that there are still insufficient charging points.
There are rumours that Chancellor Sunak may offer tax incentives to drivers of EVs in his upcoming budget on 03 March. Or rather, he might penalise drivers of ICE-powered vehicles to incentivise them to go electric. The freeze on increases in fuel duty, introduced by Mr Osborne, has now lasted for a decade. With the yawning fiscal deficit, this is a natural moment to increase fuel duty from its current level of 57.95 pence a litre on petrol and diesel.
In fiscal 2019-20, fuel duty generated £28 billion for the Treasury – that’s more than the receipts from capital gains tax, inheritance tax and alcohol duties combined. But British motorists are already amongst the highest taxed in the world and any increase in fuel duty will be seen as regressive, especially when people have been encouraged to avoid public transport and to travel to work by car during the pandemic. Hauliers will also be hit. Over time, however, as EVs displace ICE-powered cars, revenues from fuel duty will decline – and will probably have to be replaced with some form of road pricing.
Last week the Transport Secretary, Grant Shapps MP announced that renters, landlords and small businesses will be able to claim grants of up to £350 to install car chargers in their homes.
Hydrogen cars in the rear-view mirror
A British start-up building hydrogen-powered cars has been backed by Siemens (ETR:SIE) which has a track record of investing in innovative technologies. Riversimple, based in Llandrindod Wells in Wales, is developing its range of Rasa (as in tabula rasa) cars which run on hydrogen fuel cells. The two-seaters have a top speed of 60 miles per hour and a range of 300 miles. The vehicles are expected to have a 20-year working life and are designed to be recycled. The cars will be leased out rather than sold at a cost of around £500 a month.
Last October Riversimple launched a four-year £150 million funding round. The objective is to open a factory in Wales by late 2024 with the capacity to build 5,000 cars per year.
Battery technology tomorrow
One prototype could make EV batteries rechargeable in just five minutes. The breakthrough comes from Israeli battery company StoreDot. The company has designed a battery which uses so-called metalloid nanoparticles in the battery’s anode, instead of graphite. The prototype batteries were produced with Chinese partner company EVE Energy (SHE: 300014). These batteries charge much more quickly – but only given much higher-powered chargers than are used by most EV’s today. The company counts Daimler (ETR:DAI), BP (LON:BP) and Samsung (LON:BC94) amongst its backers.
A British-Australian start-up with a research centre in Cumbria has found a way of generating electricity from the decay of radioactive isotopes such as cobalt-60. Infinite Power believes that its technology, which is currently in development, will be able to slash the cost of battery manufacture. Such batteries could be used for EVs; but they might also be deployed at scale to power cities when wind power and solar power generation falls (that is on calm days and at night). Or indeed these batteries might power spacecraft on the way to Mars. Infinite Power is working with the Henry Royce Institute (UK National Institute for Advanced Materials).
Scientists at the Culham Centre for Fusion Energy in conjunction with the University of Bristol are working on power cells that harvest energy from spent nuclear fuel using man-made diamonds. These are called nano diamond batteries or nuclear diamond batteries. A spin-off company called Arkenlight is apparently working on the batteries that use this technology. (A word of warning here: its website reads as though it were badly translated into English from a foreign language).
Britain has one of the largest stockpiles of spent nuclear fuel at Sellafield, Cumbria. If this could be used to generate electricity, a colossal liability could become a huge asset. On the other hand, nothing has yet been proven. Nuclear fusion has been about to become viable for decades – and we are still waiting.
The EV battery supply chain
EV batteries require large quantities of cobalt which is mined in Canada, Australia, Zambia and the Democratic Republic of Congo. This metal is expensive. One metric tonne of cobalt today costs around $48,000. Tesla is working on EV batteries which do not use cobalt – but that may be some way off.
At present, a Tesla lithium-ion EV battery weighs more than 1,000 pounds (454 kilos). Such an EV battery typically contains about 25 pounds of lithium, 30 pounds of cobalt, 60 pounds of nickel, 110 pounds of graphite and 90 pounds of copper. Given current extraction practices, the Eurasia Review estimates that the quantity of rock that must be extracted from the earth and processed to yield the pure minerals needed to manufacture a single battery as follows. 25,000 pounds of lithium ore; nearly 30,000 pounds of cobalt ore; 6,000 pounds of nickel ore; about 1,000 pounds of graphite ore; and about 25,000 pounds of copper ore. That means that about 41 tonnes of rock must be extracted from the Earth to provide the inputs for just one EV battery.
Put like that, EVs don’t look quite as eco-friendly as we might think. If the carbon emissions of mining about 90,000 pounds of rock per car (even before production of the car body and fittings) were factored in, then production of an EV generates much more greenhouse gas than an ICE equivalent. According to the Swedish Environment Institute, 17.5 tonnes of CO2 are emitted in the manufacture of an EV battery. In comparison, a conventional ICE vehicle produces around 45 tonnes of CO2 in manufacture and on the road, if driven for 160,000 miles. And EVs are not zero carbon. For a start, they have tyres, the manufacture of which emits CO2, and which must be replaced…
Right now, there are less than 8 million EVs operating on the world’s highways. But if current projections for EV penetration are to be realised, then by 2035 there could be 125 million EVs on the world’s roads, and possibly double that. (Tesla alone aims to be producing 20 million vehicles a year by 2030). However, there is good reason to doubt that there will be enough materials in the world to manufacture 250 million EVs.
Even if the production of these critical metals could feasibly be ramped up to meet demand (with hugely negative environmental consequences), the price of these essential inputs will continue to rise. This year commodities generally are tending upwards. Over the last twelve months the price of copper has gone from $2.61 per pound to $3.82 on Monday (15 February). That implies that the cost of new EVs over time will rise in real terms much more rapidly than that of new ICE vehicles. That will further discourage middle-income motorists, especially in developing countries, from making the switch.
Then there is the issue of how those potentially toxic lithium-ion batteries will be disposed of when they come to the end of their working lives. Happily, there are numerous recycling plants in prospect in Europe and North America, pioneered by Li-Cycle, Northvolt, Ganfeng Lithium (SHE: 002460) and others.
Later this year, Li-Cycle of Canada will begin construction of a $175 million plant in Rochester NY, on the former Eastman Kodak complex. When completed, it will be the largest lithium-ion battery-recycling plant in North America. The plant will have capacity to process 25,000 tonnes of inputs, recovering 95 percent of the cobalt, nickel, lithium, and other elements. Li-Cycle will become one of the largest sources of nickel and lithium and the only source of cobalt in the US. Stockholm-based Northvolt is jointly building an EV battery recycling plant with Norway’s Norsk Hydro (OTCMKTS: NHYDY).
It will be costly to do this, however, and there will be pressure to build the cost of recycling into the initial battery purchase price, probably through taxation. (Just as the cost of nuclear power includes the cost of decommissioning the nuclear plant at the end of its economic life).
Lastly, there is the issue of the growing disparity of income and wealth in advanced economies – something which electrification is unlikely to alleviate. A recent study in California showed that EVs are driven half as much as ICE vehicles and are generally second cars (or perhaps accessories) for well-off people who like to run an ICE car as the family workhorse and enjoy excursions in the EV. Ironically, Tesla drivers are often Tesla shareholders (such is the power of its concept brand): these people have done nicely out of their EVs in more sense than one. But will Teslas become affordable for the mass market, as Mr Musk aspires? And if they do, will they lose their cachet for the rich?
For much of the 130-year history of the automobile, cars were considered luxuries; then they became aspirational; and only relatively recently did they become must-have mass market goods available to all. I suspect that the age of the EV will be one in which car ownership declines precipitously, which is not necessarily a bad thing. When ordinary folk can hail a ride in a self-driving buggy or jump on an electric-powered flying taxi piloted by a friendly robot, and indeed when most of their shopping will be delivered by whispering drones, the appeal of car ownership will diminish.
The shift from outright purchase of cars to short-term leasing deals evident in both the UK and the US is a foretaste of things to come. And why can’t we hire EVs for a few hours or days, just as people hire bicycles in major cities these days? (That is already happening as the sharing economy revs up). If one EV can be used by many travellers throughout the day that suggests that the number of vehicles on our roads will fall. (Halleluiah). Which, to say the least, puts in question the Johnson government’s obsession with roadbuilding. (I’ll return to its other most lavishly indulged white elephant – HS2 – shortly).
I’ve been listening to Bill Gates’ ruminations on our carbon neutral future this week. (His new book, How to Avoid a Climate Disaster, is being serialised on BBC Radio 4). He says that there are two numbers to start with: 51 billion is the number of tonnes of CO2 currently spewed into the atmosphere every year; and zero is the target, sometime around the 2060s or theerabouts. To achieve that we would have re-engineer almost everything.
Somehow, I don’t think the lithium-ion battery will be the solution. Within 10-15 years it will be seen as an intermediate technology. But canny investors will enjoy the ride.
Where does Ceres Power sit in this argument, different type of technology also aimed at automotive sector and with established links with Bosch.
Ilika (IKA) the Southampton University spinoff is developing solid state batteries with a much higher power density. this has the potential to be a disruptive technology.
Ceres Power, fuel cell operates at 600 degrees C, may be good for trains etc,, but I doubt it for the family car,, ,,, but there are other fuel cell technologies much more suitable for cars.
In this article when you consider 41 tons of rock is moved to make on EV car battery , then the case for hydrogen fuel cells for family car only be comes stronger. Only a small EV battery is required in a hydrogen vehicle.
Kids (young adults) these days are whizzing around on scooters. Inexpensive, they have no plans to buy a car.
If they’re going far: uber.
I used Grab taxi extensively while in Malaysia – couple of pounds per trip. And used again at the end of the metro line. Efficient.
Who needs a car?